Troubleshooting Your Equipment: When to Call for Packaging Machine Repair
Troubleshooting Your Equipment: When to Call for Packaging Machine Repair
Blog Article
Quick and Reliable Product Packaging Equipment Fixing Services to Lessen Downtime
In the competitive landscape of production, the performance of product packaging procedures rests on the integrity of machinery. Quick and dependable repair services are crucial in reducing downtime, which can bring about considerable monetary losses and operational obstacles. Recognizing the value of timely interventions and the role of expert technicians can transform exactly how businesses approach repair and maintenance. Browsing the myriad alternatives readily available for fixing solutions can be difficult. What factors should companies consider to guarantee they are making the ideal selection for their functional demands?
Importance of Timely Repair Works
Timely repairs of packaging makers are important for keeping operational efficiency and decreasing downtime. In the hectic atmosphere of production and product packaging, even small breakdowns can lead to significant hold-ups and performance losses. Dealing with problems promptly makes sure that equipments run at their optimal capacity, consequently safeguarding the circulation of procedures.
Additionally, timely and normal upkeep can avoid the acceleration of minor troubles right into major malfunctions, which frequently incur higher repair service expenses and longer downtimes. An aggressive approach to machine repair service not only protects the stability of the devices however additionally enhances the overall reliability of the production line.
Additionally, prompt repair work add to the durability of packaging machinery. Equipments that are serviced immediately are less most likely to suffer from too much wear and tear, allowing companies to optimize their investments. This is especially vital in markets where high-speed product packaging is important, as the need for regular performance is paramount.
Advantages of Reliable Solution Companies
Dependable solution suppliers play an essential duty in ensuring the smooth operation of product packaging machines. Their competence not only improves the efficiency of fixings however additionally adds dramatically to the durability of equipment.
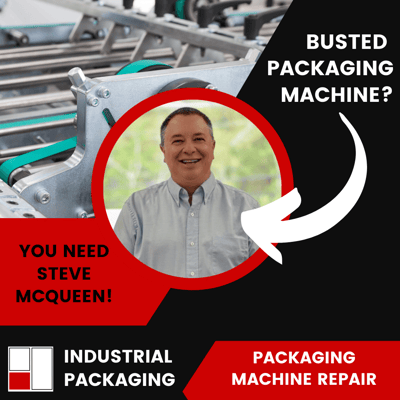
In addition, a respectable company offers comprehensive assistance, consisting of training and guidance for personnel on equipment procedure and maintenance ideal practices. This not only encourages staff members but also cultivates a society of safety and performance within the company. In general, the benefits of involving reliable provider prolong past immediate repairs, favorably influencing the entire functional process of product packaging procedures.
Usual Packaging Equipment Concerns
In the world of product packaging operations, different problems can jeopardize the performance and functionality of makers (packaging machine repair). One more typical issue is misalignment, which can trigger jams and uneven packaging, impacting product top quality and throughput.
Electric troubles can likewise interfere with product packaging operations. Faulty electrical wiring or malfunctioning sensing units may result in irregular equipment behavior, causing hold-ups and raised operational expenses. Additionally, software program glitches can read hinder the machine's shows, leading to functional inefficiencies.
Inconsistent product circulation is another important concern. This can develop from variants in item shape, weight, or dimension, which might influence the maker's ability to manage items accurately. Insufficient training of drivers can intensify these problems, as inexperienced personnel might not identify very early indicators of malfunction or may misuse the devices.
Resolving these usual packaging equipment issues quickly is vital to maintaining efficiency and making sure a smooth operation. Normal examinations and aggressive maintenance can dramatically reduce these issues, cultivating a reputable product packaging atmosphere.
Tips for Reducing Downtime
To decrease downtime in product packaging operations, carrying out a proactive maintenance strategy is vital. Regularly set up upkeep checks can identify potential problems prior to they intensify, making sure makers operate successfully. Establishing a routine that consists of lubrication, calibration, and assessment of vital components can significantly lower the frequency of unforeseen malfunctions.
Educating personnel to run machinery appropriately and acknowledge early indication of breakdown can additionally play a crucial duty. Encouraging drivers with the knowledge to carry out basic troubleshooting can avoid minor issues from causing major hold-ups. Furthermore, maintaining an efficient supply of essential extra components can expedite repair services, as awaiting components can bring about extended downtime.
In addition, recording machine performance and upkeep activities can help identify patterns and frequent troubles, permitting for targeted treatments. Including innovative tracking innovations can offer real-time information, making it possible for predictive upkeep and decreasing the danger of sudden failings.
Last but not least, fostering open communication in between operators and maintenance groups guarantees that any type of irregularities are quickly reported and dealt with. By taking these proactive actions, companies can boost functional performance and considerably lower downtime in packaging processes.
Choosing the Right Repair Service Solution
Choosing the proper fixing service for packaging devices is a critical decision that can dramatically affect functional efficiency. Begin by examining the company's experience with your specific type of packaging equipment.
Following, take into consideration the company's online reputation. Seeking feedback from various other services within your industry can give understandings right into dependability and quality. Certifications and partnerships with acknowledged devices makers can additionally suggest a dedication to quality.
Additionally, examine their action time and schedule. A solution copyright who can offer timely assistance decreases downtime and maintains manufacturing circulation stable. It's also essential to ask about guarantee and service guarantees, which can reflect the confidence the company has in their job.
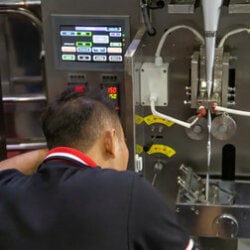
Final Thought
In conclusion, the value of trusted Extra resources and fast product packaging maker repair service services can not be overemphasized, as they play an important function in minimizing downtime and making certain operational performance. Executing aggressive maintenance techniques and spending in staff training additional enhances the long life of product packaging machinery.
Prompt fixings of packaging devices are essential for keeping functional performance and decreasing downtime.In addition, prompt repair work add to the durability of product packaging equipment. Generally, the advantages of engaging dependable service carriers expand past immediate repair services, favorably impacting the entire functional operations of packaging processes.
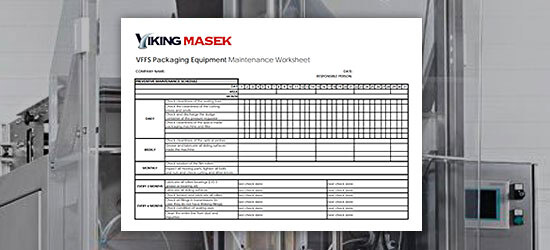
Report this page